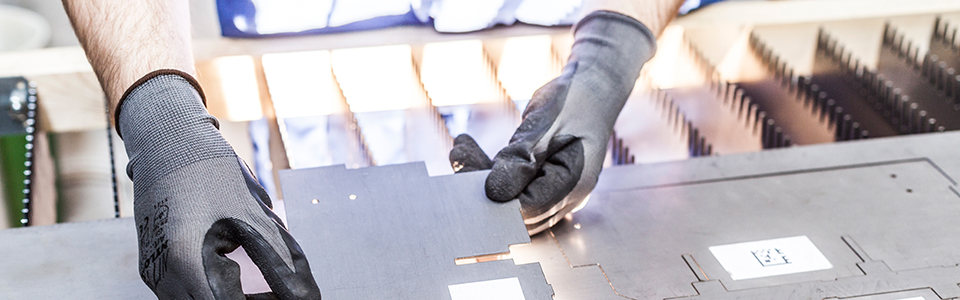
Auftrag abholen, Teile zusammensuchen, Material ans Band bringen und Teile abtransportieren – solche indirekten Prozesse kosten in der Blechbearbeitung jede Menge Zeit und Ressourcen. Hier lassen sich mit Industrie 4.0 Einsparungen erzielen. Welche Optimierungspotenziale sich bei welchen Prozessen ergeben, haben die Firma Trumpf und das Fraunhofer IPA in einer Studie analysiert.
Bis vor einigen Jahren war in der industriellen Blechbearbeitung noch die Teilezeit ausschlaggebend. Die Entscheidung einer Firma für oder gegen eine Maschine hing hauptsächlich von der Dauer des Bearbeitungsprozesses ab. Heutzutage sind die meisten Anlagen allerdings mit hocheffizienten Technologien, z. B. Lasertechnik, ausgestattet und arbeiten so schnell, dass die vor- und nachgelagerten Prozesse nicht mehr hinterherkommen.
Um die Blechbearbeitung mit Industrie-4.0-Technologien effizienter zu gestalten, startete Trumpf mit dem Fraunhofer IPA im Jahr 2015 das langfristige Projekt »Lab flexible Blechbearbeitung«. Die entwickelten Lösungen sollen anschließend unter dem Begriff »TruConnect« bei Trumpf eingesetzt und vermarket werden. U.a. führten die Partner eine Studie durch, die aufzeigen sollte, welche Potenziale sich mit digitalen Anwendungen ergeben.
Für ihr Forschungsvorhaben besuchten die IPA-Wissenschaftler mit Trumpf-Mitarbeitern und der studentischen Unternehmensberatung Emendo 25 Trumpf-Kunden aus der Blechbearbeitung. Hier untersuchten sie die einzelnen Arbeitsschritte nach Lean-Kriterien und zeigten u.a. mit Wertstromanalysen und Layouts auf, wo Verschwendungen entstehen. Nachdem die Prozesse analysiert waren, errichteten die IPA-Forscher einen Demo-Arbeitsplatz in ihrem »Applikationszentrum Industrie 4.0«, der die Wirklichkeit der meisten Unternehmen aus der Blechbearbeitung abbildet. Hier sollten die Industrie-4.0-Lösungen getestet und dem IST-Zustand gegenübergestellt werden.
Der anschließende Vergleich bestätigte die Wirksamkeit der Anwendungen: »Je nach Kundensituation haben wir pro Auftrag Zeiteinsparungen von 28 bis 51 Prozent erzielt«, freut sich der damalige Projektleiter Ulrich Schneider. Für einzelne Prozesse ergeben sich sogar noch größere Potenziale. Beim Zusammenstellen der Materialien für einen Auftrag, der Kommissionierung, ermittelten sie eine Zeitersparnis von 85 Prozent. Auch beim Auffinden von Blechbauteilen war die optimierte Lösung um 42 Prozent schneller. Neue Technologien, die für das Absortieren der Teile an der Laserschneidmaschine eingesetzt wurden, reduzierten die Dauer um 48 Prozent gegenüber der Laufzettelvariante. Neben der Zeitersparnis punkteten die Industrie-4.0-Lösungen mit einer höheren Ergebnisqualität. »Beispielsweise konnte beim Absortieren mit automatischer Teileerkennung und Buchung die Fehlerhäufigkeit von durchschnittlich 1,5 auf 0 Prozent gesenkt werden«, weiß Schneider. Überproduktionen, die seither aufgrund eingeplanter Verluste bewusst angefertigt wurden, lassen sich damit vermeiden.