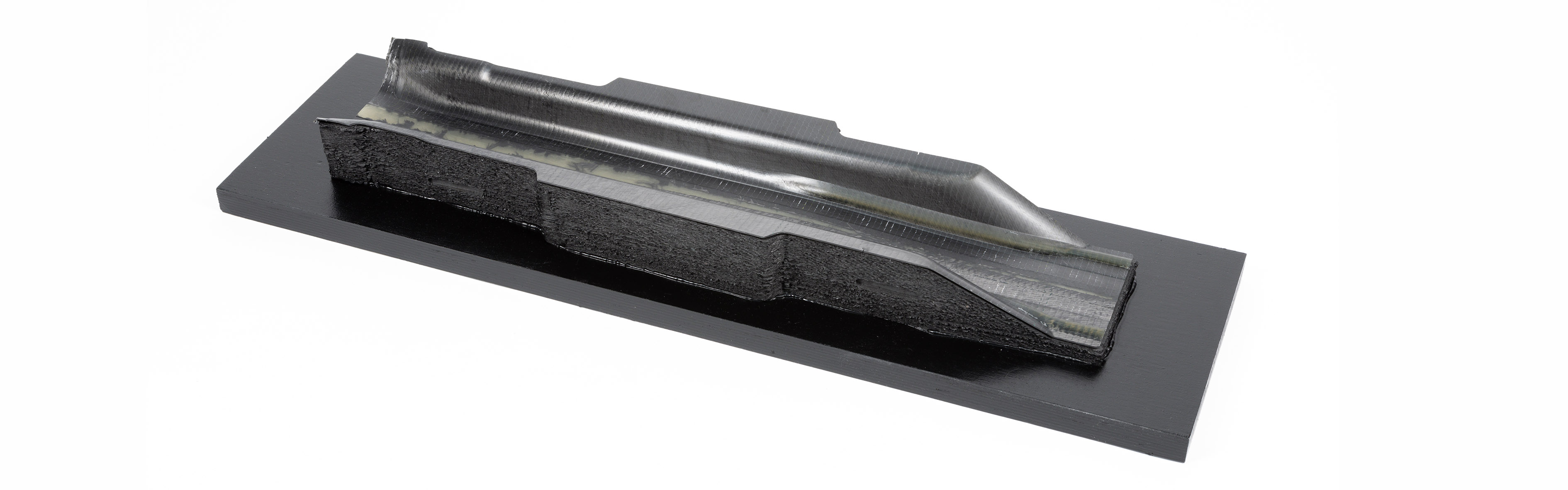
Im Forschungsprojekt »Entwicklung 3D-gedruckter, hochintegrativer Spannschablonen für CFK-Bauteile« erfolgte die prototypische Fertigung einer funktionsintegrierten Spannschablone für die spanende Nachbearbeitung von Bauteilen aus kohlenstofffaserverstärkten Kunststoffen (CFK). Durch den kombinierten Einsatz additiver und subtraktiver Fertigungsverfahren, Topologieoptimierung sowie einem hohen Grad an Funktionsintegration konnten neue Ansätze zur effizienten Herstellung von Spannschablonen aufgezeigt werden.
CFK-Bauteile werden endkonturnah hergestellt, sodass diese nur im Bereich des Bauteilrandes und zur Funktionalisierung, bspw. zur Einbringung von Bohrungen oder Ausschnitten, spanend endbearbeitet werden müssen. Aufgrund der meist offenen und großflächigen Bauteilgestaltung sind diese sehr labil und neigen trotz der hohen Steifigkeit zu Schwingungen, was sich negativ auf die Werkzeugstandzeit und Bauteilqualität, z.B. die Maßhaltigkeit und Kantenqualität, auswirkt. Um derartige Effekte bei der Endbearbeitung zu vermeiden, werden Spannschablonen eingesetzt, auf denen die CFK-Bauteile vollflächig aufliegen und mittels Vakuum schwingungsarm aufgespannt werden können. Diese Spannschablonen werden typischerweise aus dem Vollen, also aus großen Kunststoff- oder Metallblöcken gefräst, wobei sehr viel Material abgetragen werden muss, was mit einem hohen zeitlichen und anlagentechnischen Aufwand, hohen Kosten und einer schlechten Ressourceneffizienz verbunden ist. Zudem sind Funktionalitäten wie Fräs- oder Absaugungskanäle durch die Spannschablone äußert aufwendig in der Herstellung, da dies eine komplexe, mehrseitige Bohr- und Fräsbearbeitung erfordert. Des Weiteren sind die massiven Formgebungswerkzeuge und Spannschablonen sehr schwer und daher oft nur mit Flurförderfahrzeugen zu transportieren.
Aus den genannten Gründen wurden im Rahmen des Brückenprojekts von den beteiligten Forschungsinstituten Möglichkeiten zur effizienten Herstellung hochintegrativer Spannschablonen durch den kombinierten Einsatz additiver und subtraktiver Verfahren, also dem Druck der Vorrichtungen mittels extrusionsbasiertem 3D-Druck und der anschließenden spanenden Nachbearbeitung von Funktions- und Auflageflächen, untersucht und eine Demonstrator-Spannschablone gefertigt. Die Vorteile des extrusionsbasierten 3D-Drucks liegen in der hohen Austragsleistung und der Verwendung eines günstigen Spritzgussmaterials, sodass eine schnelle und wirtschaftliche Herstellung individueller Endprodukte ermöglicht wird. Durch den schichtweisen Aufbau erlaubt die additive Fertigung nahezu unbegrenzte Gestaltungsmöglichkeit und ermöglicht daher eine einfache Integration von Funktionalitäten wie Vakuumfelder, Fräs- und Absaugkanälen. Durch die gezielte Einbringung von Hohlstrukturen lassen sich zudem signifikante Gewichtseinsparungen realisieren, die zu einer größeren Materialeffizienz, kürzeren Druckzeiten sowie einer leichteren Handhabung der Spannmittel führen.
Schon jetzt lässt sich das Potenzial von additiv gefertigten Spannmitteln für die spanende Endbearbeitung von CFK-Bauteilen verdeutlichen. Weitere Untersuchungen zur generellen Prozesstauglichkeit additiv gefertigter Spannmittel für reale CFK-Bauteile, vor allem mit Blick auf die besonderen Anforderungen der Bauteilgrößen in der Luft- und Raumfahrtindustrie sowie Windenergie, sind Gegenstand aktueller und zukünftiger Forschungsarbeiten.