Sitzend montieren leicht gemacht
Hocker ins Auto heben, montieren, Hocker herausheben, im nächsten Auto weitermontieren. Diesen Vorgang wiederholen Monteure in der Autombilbranche mehrere hundert Mal am Tag – mit gesundheitlichen Risiken. Um seine Mitarbeiter zu entlasten, hat VW das Fraunhofer-Institut für Produktionstechnik und Automatisierung beauftragt, extraleichte ergonomische Montagehocker zu entwickeln. Mithilfe generativer Fertigungsverfahren und hybridem Leichtbau ist es den Wissenschaftlern gelungen, das Gewicht der Sitzgelegenheiten um die Hälfte zu reduzieren.
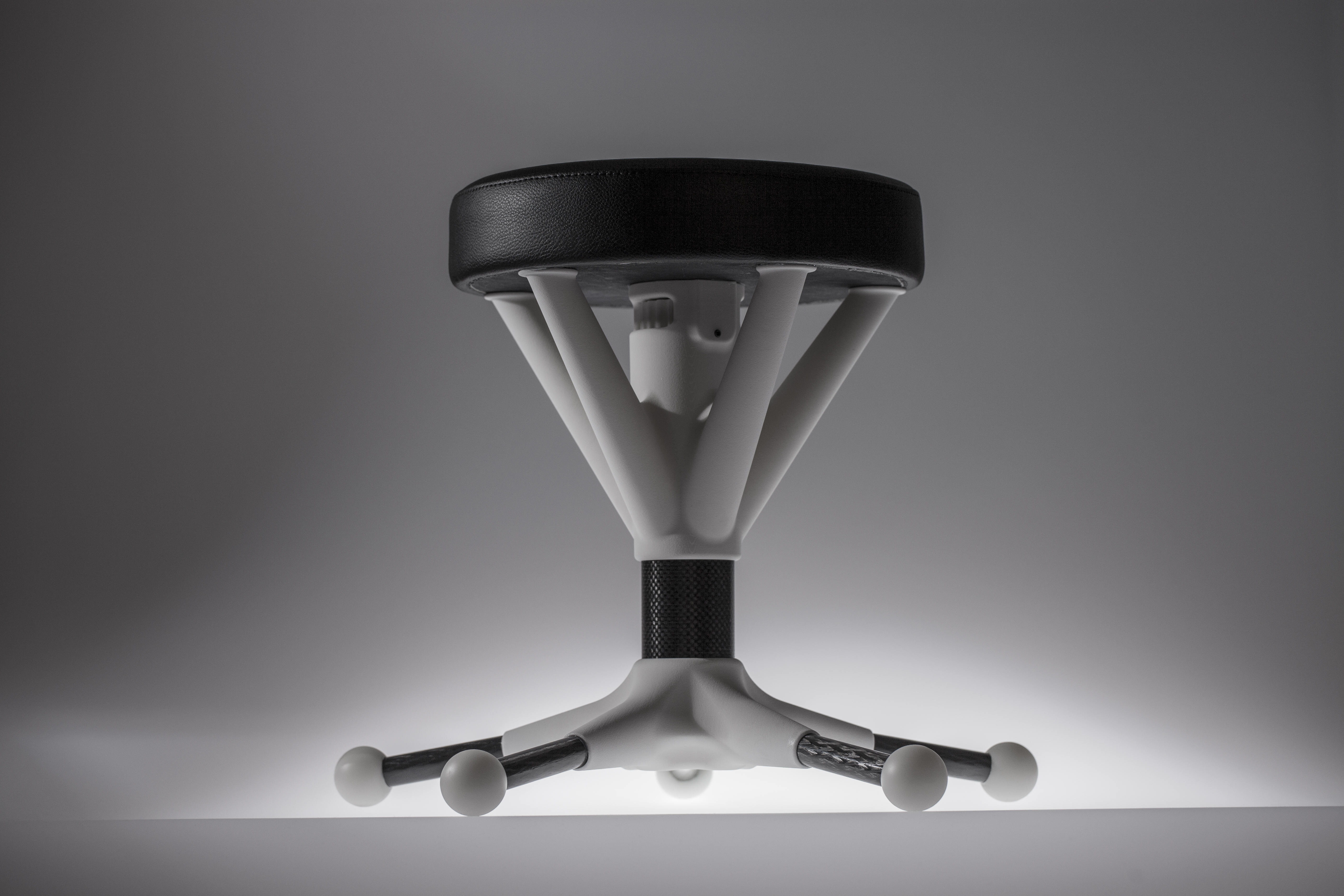
Wie die meisten Automobilhersteller produziert VW in Serie. In der Fertigungslinie durchlaufen die Fahrzeuge verschiedene Montagestationen. Die Monteure sind dafür zuständig, bei jeder Station bestimmte Teile anzubringen, beispielsweise Lenkrad, Rückspiegel oder Radio. Da im Fahrzeuginnenraum im Sitzen gearbeitet wird, müssen die Monteure ihre Hocker nach jedem Montagevorgang aus dem Auto heraus und ins nächste hinein heben. Je schwerer die Sitzgelegenheit, desto stärker werden Skelett, Muskeln und Gelenke langfristig beansprucht. Leichtere Montagehocker schaffen bessere Produktionsbedingungen, was sich in einer höheren Produktqualität mit geringerer Fehleranfälligkeit niederschlägt.
Der Aufgabenstellung von VW, extraleichte Montagehocker zu entwickeln, haben sich Steve Rommel und Raphael Geiger aus der Abteilung »Generative Fertigung« angenommen. Dabei war es ihnen wichtig, Technologien zu verwenden, die den
hohen Belastungen des Montagealltags standhalten. »Da bei der Montage mit schweren Werkzeugen gearbeitet wird, müssen die Hocker aus Sicherheitsgründen nicht nur leicht, sondern auch stabil sein«, erklärt Geiger.
Generative und hybride Fertigungsverfahren als Schlüsseltechnologie
Bei den Montagehockern für VW setzten die Wissenschaftler »generativen hybriden Leichtbau« ein, eine Kombination generativer Fertigungsverfahren mit ultrafesten kohlenstofffaserverstärkten Kunststoff-Halbzeugen. Der Vorteil: minimales Gewicht bei maximaler Belastbarkeit. »Generative Fertigungsverfahren ermöglichen uns ein Höchstmaß an Gestaltungsfreiheit. Somit können wir komplexe und lastoptimierte Strukturen anfertigen. Da sich 3D-gedruckte Bauteile passgenau an weitere Werkstücke anpassen lassen, sind die Endprodukte zudem besonders stabil«, erläutert Rommel. Als Ausgangsmaterial verwendeten die Wissenschaftler Kunststoffpulver, welches mithilfe des Fertigungsverfahrens »Selektives Lasersintern (SLS)« in Form gebracht wird. Den hybriden Ansatz verwirklichten sie, indem sie ultraleichte Trägerelemente aus kohlenstofffaserverstärktem Kunststoff integrierten.
Tatsächlich sind die neuartigen Montagehocker echte Fliegengewichte: Mit weniger als 2,3 Kilogramm wiegt ein Exemplar weniger als halb so viel wie sein Vorgängermodell. VW hat die Entwicklung komplett übernommen und setzt derzeit die Montagehocker in der Produktion ein. Bei über 100 Produktionsstätten weltweit ergibt sich damit ein enormer Nutzwert.
Generativ hybride Produktionstechnologien bieten Potenziale für zahlreiche Branchen. »Das Verfahren ist für die Flugzeugindustrie, den Maschinenbau oder die Medizin- und Biotechnik vielversprechend«, so Geiger. Eine Ersparnis von einem Kilogramm Gewicht besitzt in der Luftfahrt einen Gegenwert von 500 Euro. Ein durchschnittliches Passagierflugzeug umfasst 200 Plätze. »Bei einer Gewichtsersparnis von 2,5 Kilogramm pro Sitz ist der Nutzwert für den Kunden erheblich«, erläutert Geiger.