Erweitertes Lean-Konzept für wirtschaftliche und ökologische Produktion
Nur schlank reicht nicht mehr
Im Projekt »Eco Lean Compass« hat das Fraunhofer IPA eine Methode entwickelt, die neben den ökonomischen Aspekten des Lean Managements auch ökologische Gesichtspunkte berücksichtigt. Unternehmen verbessern dadurch nicht nur die Effizienz ihrer Wertschöpfungskette, sondern gleichzeitig auch ihre Umweltbilanz. Das neue Eco-Lean-Konzept steht dem produzierenden Gewerbe ab sofort zur Verfügung.
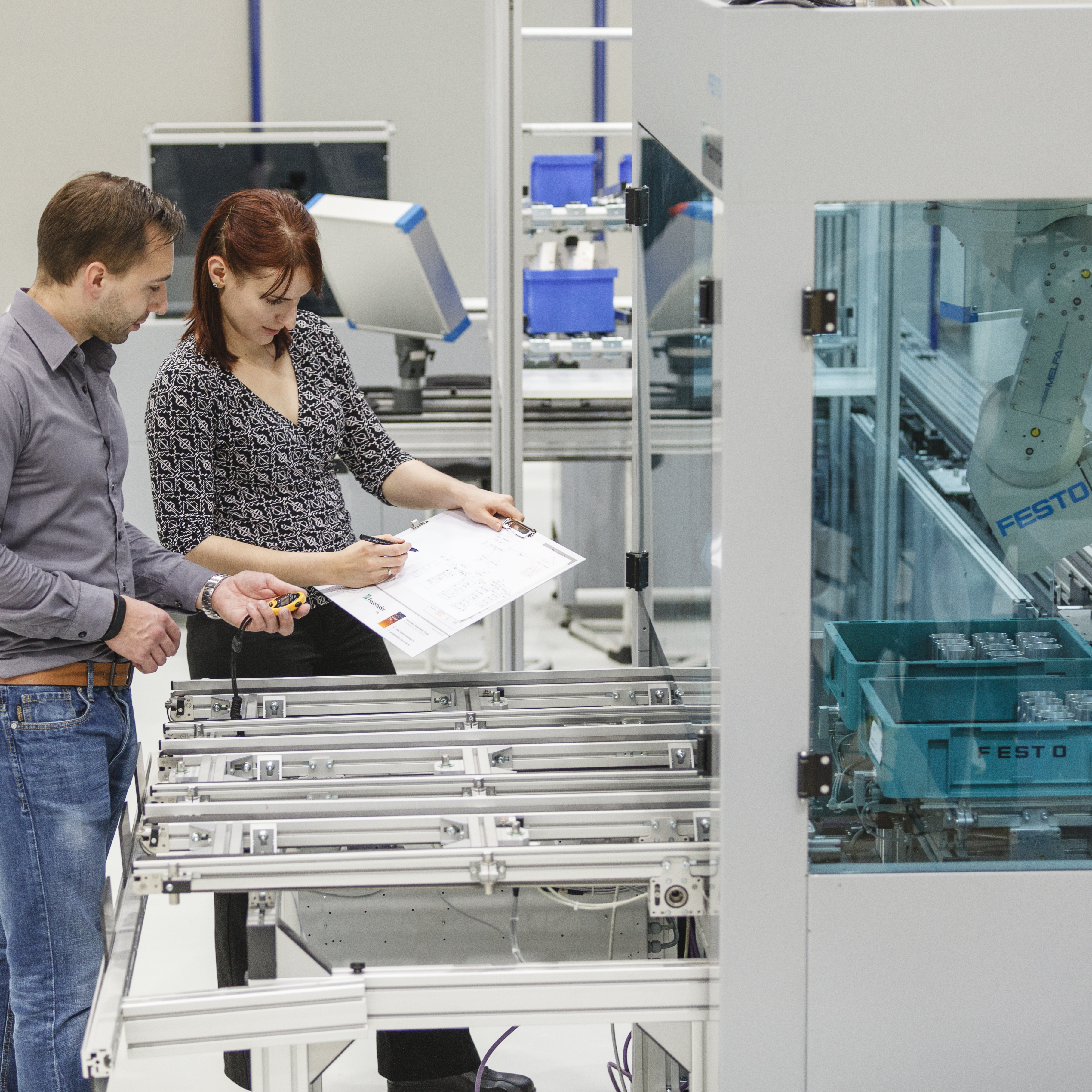
Im klassischen Lean Management geht es darum, die Produktion so schlank wie möglich zu gestalten. Der Ansatz sieht vor, überflüssige Tätigkeiten abzuschaffen und die Prozesse optimal aufeinander abzustimmen. Gängige Methoden wie Wertstromanalysen erzielen in erster Linie mehr Transparenz, lassen die Umweltbilanz aber außen vor. »Gerade diese wird aber angesichts zunehmend kritischer Konsumenten und steigender Rohstoffpreise immer wichtiger«, informiert Robert Miehe, Projektleiter am Fraunhofer IPA.Ziel des bis 2017 laufenden Projekts »Eco Lean Compass« ist es daher, den Lean-Ansatz
so zu erweitern, dass die Effizienz der Produktion zwar gesteigert, deren negative Umweltauswirkungen aber reduziert werden. Dafür haben die Experten die gängigen Lean-Methoden mit Konzepten der Ressourceneffizienz kombiniert. »Zu den Messgrößen ›Zeit‹ und ›Stabilität der Prozesse‹ kommt ›Ressourceneffizienz‹ als weitere Restriktion hinzu«, erläutert Miehe. Ein wesentlicher Unterschied sei zudem das differenzierte Verständnis der Verschwendung. »Beim Eco Lean Management fallen darunter nicht nur Tätigkeiten, sondern auch Ressourcen. Jedes Material, das nicht im Produkt verbleibt, gilt z. B. als verschwendet«, informiert Miehe. Berücksichtigt werde auch die strategische Komponente der Produktion, z. B. die Produktentwicklung und die Fertigungssystemplanung.
Ohne Bestandsmanagement werden Ressourcen oft verschwendet
Erste Tests haben die Experten bei einem mittelständischen Unternehmen im Werkzeugbau schon erfolgreich durchgeführt. Bei der Analyse habe sich schnell gezeigt, dass wenig Transparenz über die eingesetzten Stoffe und verbrauchten Energiemengen vorliegt. »Wie viele Firmen der Branche verfügte unser Partner über kein richtiges Bestandsmanagement. Im Lager arbeitet z. B. nur ein Mitarbeiter, der Ressourcen wegwirft, wenn sie länger nicht gebraucht werden. Ist dieser im Urlaub, benötigt das Personal wiederum viel Zeit, Material zu suchen«, berichtet Miehe. Missstände wie diese können die IPA-Wissenschaftler mit ihrem neuen Konzept schnell und einfach beheben. »Unserem Partner konnten wir z. B. mit der erweiterten 5S-Methode aufzeigen, wie er seine Ressourceneffizienz um 20 Prozent steigern kann«, berichtet Miehe.
Die IPA-Wissenschaftler bieten das Konzept ab sofort als Dienstleistung an. Das Verfahren eignet sich für alle Firmen, die in der Stückgutfertigung tätig sind. »Dabei lassen sich vor allem einfache Low-Cost-Lösungen identifizieren und umsetzen«, informiert Miehe. Insbesondere für KMU ergeben sich dadurch Potenziale, weiß der Projektleiter.