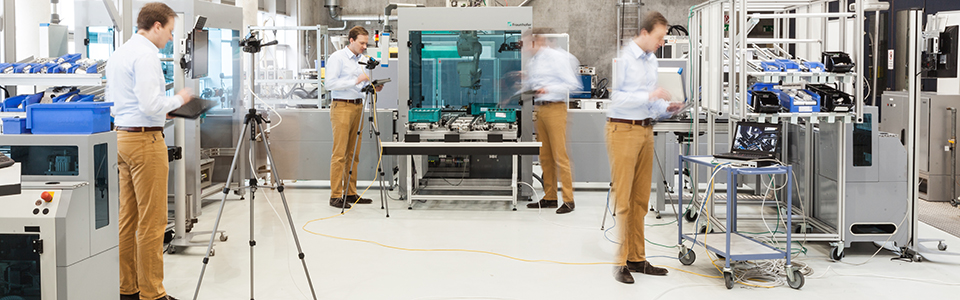
Das Fraunhofer IPA analysierte bei dem Automobilzulieferer Adient die Ursachen von Stillständen und Ausschuss eines schnell taktenden, automatisierten Fertigungssystems zur Herstellung von Rastbeschlägen für Fahrzeugsitze. Die datengetriebene Analyse führte zu Optimierungsmaßnahmen, welche die Produktivität der Fertigungsanlage nachhaltig erhöht haben.
Bei einer Vielzahl von miteinander verbundenen Fertigungsschritten mit einer Taktzeit von drei Sekunden sind die Ursachen von Stillständen und Ausschuss nicht einfach zu identifizieren. Mit Hilfe der sogenannten »Smarten Systemanalyse und -optimierung« war es möglich, die Ursachen auch von komplexen Fehlern genau zurückzuverfolgen. Im Rahmen des Pilotprojekts bei Adient griffen die Wissenschaftler/-innen Signaldaten von Maschinensteuerungen (Siemens S7-400) und zusätzlich integrierten Sensoren (Cognex-Kamerasprüfysteme, Temperatursensoren) und Kameras zur Objekterkennung ab. Sie nutzten eigens entwickelte Auswertungsalgorithmen zur Fehler- und Ursachenanalyse und konnten so in kürzester Zeit Optimierungspotenziale der OEE (Overall Equipment Effectiveness = Gesamtanlageneffektivität) in Höhe von 8,6 Prozent ableiten und mit Hilfe einer Simulation verifizieren.
Im Laufe des Projekts wurden bereits erste „Quick-Wins“ in Höhe von 3,5 % implementiert. Dabei wurden unter anderem Potenziale zur Anpassung von Steuerungs-Parametern identifiziert, welche ohne den datengetriebenen Ansatz in den Tausenden von Steuerungsvariablen und Ablaufabhängigkeiten nicht entdeckt worden wären. Gerade komplexe Fehlerbilder, die sich durch gegenseitige Wechselwirkungen zwischen mehreren nacheinander folgenden Fertigungsschritten ergeben, konnten so aufgedeckt werden. Auch die Auslegung von Puffern sowie die Ausschleusungsstrategie von Nacharbeit- und Ausschuss-Werkstücken konnte quantifiziert und im zweiten Schritt optimiert werden.
Adient möchte diese Methode nun auch für größere Produktionsanlagen mit mehr als 50 beteiligten Fertigungs- und Montageprozessen übernehmen und in Zukunft kontinuierlich analysieren und Aussagen über aktuell vorliegende komplexe Fehlerbilder echtzeitnah aufdecken. Die IPA-Wissenschaftler/-innen arbeiten bereits an einer skalierbaren Version ihres Werkzeugs.