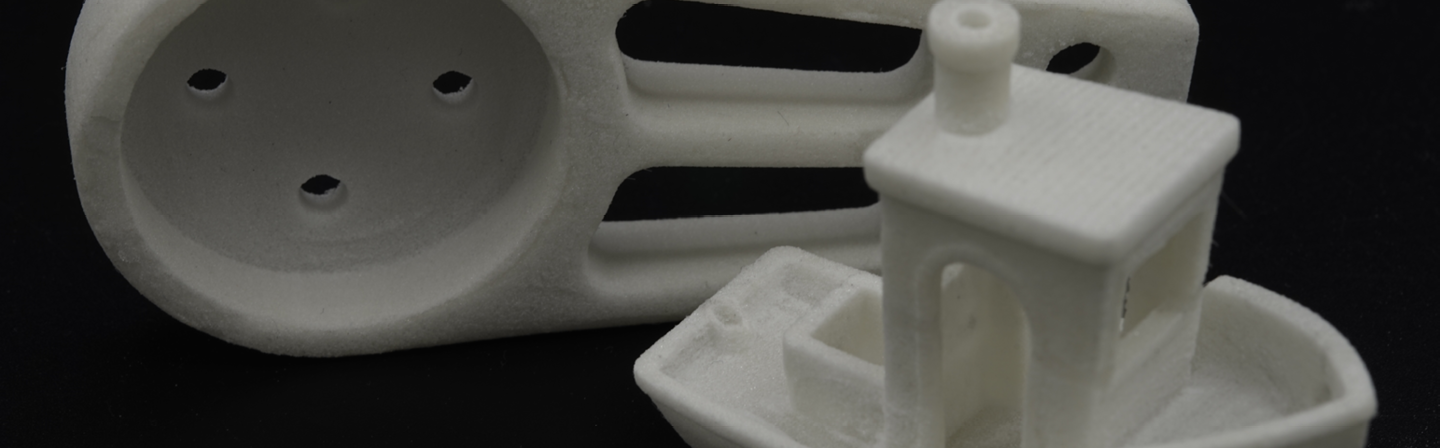
The project examined how polycarbonate (PC), a new type of plastic, behaves during the PBF-LB/P process. Innovative strategies were developed to process the plastic at low installation temperatures.
Lean Plastics Technologies GmbH initiated a feasibility study to develop a new type of powder for the highly relevant industrial 3D printing process, PBF-LB/P. Currently, polyamide 12 or 11 is used almost exclusively (90% of the time). However, innovative PBF powder types are required to enable 3D printing technology for other applications. PC, an amorphous thermoplastic, was tested for production and processing. The powder must meet high standards: it must have a precise particle size distribution. (approximately 50 µm) and free-flowing to enable the application of uniform layers in the printer. During the process, the laser must be able to quickly fuse it into dense layers. As part of a ZIM feasibility study, Lean Plastic Technologies' powder production technology was tested with PC and examined by Fraunhofer IPA regarding processing in the PBF-LB/P process.
Fraunhofer IPA set the ambitious goal of developing the most sustainable process possible. Typically, the installation temperature is close to the softening temperature, but in this case, it should be significantly lower. This would prevent polymer aging and enable the complete reuse of unmelted powder.
After Lean Plastics Technologies produced a free-flowing powder, initial processing trials were conducted at Fraunhofer IPA using a small industrial plant. The initial process parameters were determined experimentally using simple sample geometries. It quickly became apparent that the powder had great potential for processing. After optimizing the laser power, scan speed, and hatch distance, the first demo parts were produced at moderate installation temperatures. After three months of intensive research, Fraunhofer IPA scientists demonstrated the powder's good processability using test geometries. The unprinted powder showed no signs of aging and could be fully reused without any loss of quality.
The results of the feasibility study have been validated for the customer, showing that processing is possible and identifying areas of future development that will present challenges. The powder and process can now be further developed in a follow-up project. Questions regarding processability on standard industrial systems must be answered. Extensive component testing and post-processing options must also be considered. Once feasibility has been successfully demonstrated, the medium-sized company will need to invest in further research with improved prospects of success.
»The project results have demonstrated that PC has great potential for powder-based 3D printing. Thanks to the knowledge we gained from the feasibility study, it's easier for us, as a medium-sized company, to invest more in further research.«
Matthias Düngen (Managing Director of Lean Plastics Technologies GmbH)