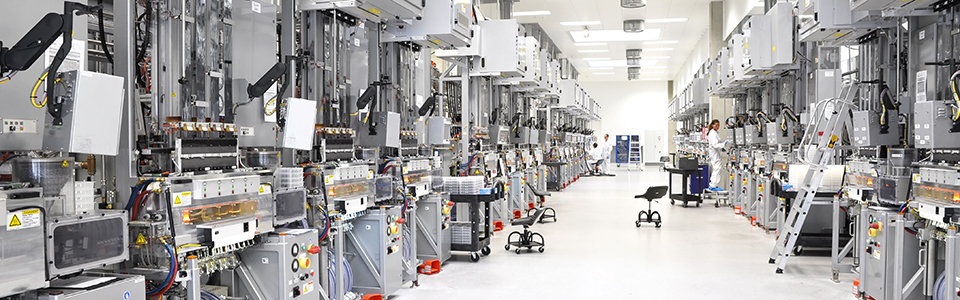
At SCHOTT Schweiz AG, Fraunhofer IPA applied a patented method to examine the highly-automated syringe manufacturing system for errors and their causes, or to find out where these errors were being reproduced in the networked system. From this analysis, a new manufacturing system concept was derived which is capable of improving overall equipment effectiveness by 10 percent for existing systems, and by around 10-30 percent for future systems.
The process for optimizing the manufacturing system started with a so-called “smart system analysis”. This method can be easily and flexibly integrated into a running production system. Several cameras then observe selected features during each process step, even if they are executed at high speed. Any discrepancy arising is traced. The software assesses whether these discrepancies will cause immediate losses or ones during later process steps. This makes it easier to pinpoint causes.
The IPA scientists compared the analysis results with benchmarks from similar production facilities. Using this information, they designed an ideal manufacturing system, including simulative dimensioning, and then compared the concept both from an economic and technical point of view. SCHOTT Schweiz AG can now operate existing as well as future systems more effectively.
“Through the project, we know exactly how much potential can still be exploited from our existing system. In addition, we can benchmark future manufacturing systems based on the ideal concept developed by Fraunhofer IPA.”
Michael Feldhaus
Head of Production Sterile Technology
Smart system analysis based on SCHOTT