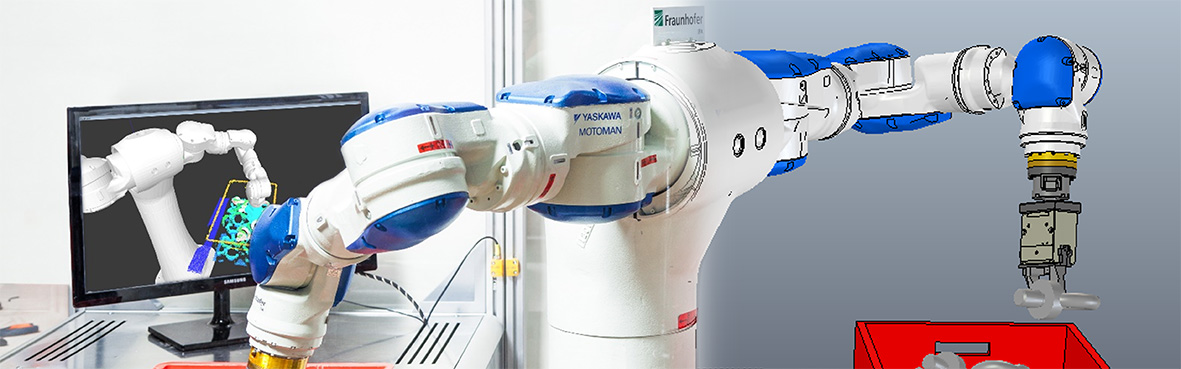
In the “Deep Picking” project, modular and adaptable software and hardware solutions are being developed for picking and depalletizing known and unknown objects that are delivered in different states during production processes. The solutions can be integrated and taught in quickly and robustly.
The aim of the “Deep Picking” project is to integrate new technologies that increase the degree of automation in handling in order to exploit economic and qualitative potential. To this end, the IPA experts are developing new handling technologies to make depalletizing and order picking tasks as robust and flexible as possible.
Up to now, handling workpieces and products has been both a challenging and important task in intralogistics and production. The biggest problem is the enormous diversity of product and workpiece variants. This makes it difficult to tailor a system to the respective product, which is crucial for a robust process. Furthermore, handling in automated processes is usually designed to be workpiece-specific. Conventional handling tasks therefore reach their limits, especially where unknown objects are concerned.
By using machine learning, the IPA solution creates new technologies that enable unknown objects to be handled. To increase the automation potential, these technologies are particularly necessary when it comes to depalletizing processes in intralogistics and kitting applications in production plants.
The developed technologies complement Fraunhofer IPA's extensive range of gripping planning software. If your use case also calls for a tailored gripping solution, please get in touch with us.