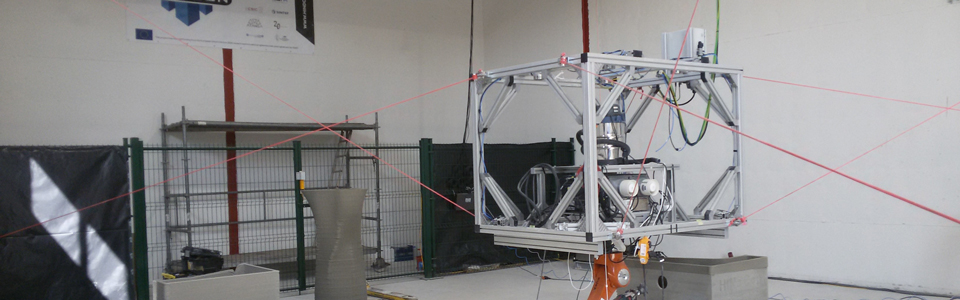
A large, easily scalable workspace and a lean system:
Within the Hindcon project (Hybrid INDustrial CONstruction), a hybrid machine for 3D-printing of concrete materials has been developed. It reduces costs and environmental pollutions which arise during the production of concrete and the transport of large components. With the development of an »on-site production environment«, components do not need to be stored temporarily or delivered to their destination. Furthermore, the additive process saves material.
The resulting »all-in-one« machine consists of an extruder moved by a cable-driven parallel robot that has been developed at Fraunhofer IPA. The exact positioning of the extruder is carried out via the appropriately designed interface. The construction is modular and consists of only a few components: the winches, the cables and the platform. Compared to other systems for large workspaces, such as gantry robots, the cable-driven parallel robot is easy to transport and reconfigure.
The concrete parts are produced by additive manufacturing and further processed by subtractive manufacturing. The combination of both processes enables the efficient production of individual concrete components with free-form surfaces, which could only be produced at great expense using conventional formwork methods.
The following video shows the final demonstrator of the project during the production of prefabricated building material.