Parts2Clean 2017: Fraunhofer IPA presents details of the process chain from cleaning through analytics all the way to packaging in ultra-clean environments.
Cleaning is just the beginning
It is more complicated than many might think to clean components for industry. Expert knowledge is required in selecting the correct cleaning process, cleanliness analysis and packaging. Moreover, industry-specific regulations and the requisite infrastructure are additional factors involved. Fraunhofer IPA is the only institution in Germany to offer the entire process chain in an ultra-clean environment. Experts will present details of this at Parts2Clean, an international trade fair for industrial parts and surface cleaning, which is being held October 24–26, 2017 in Stuttgart, Germany.
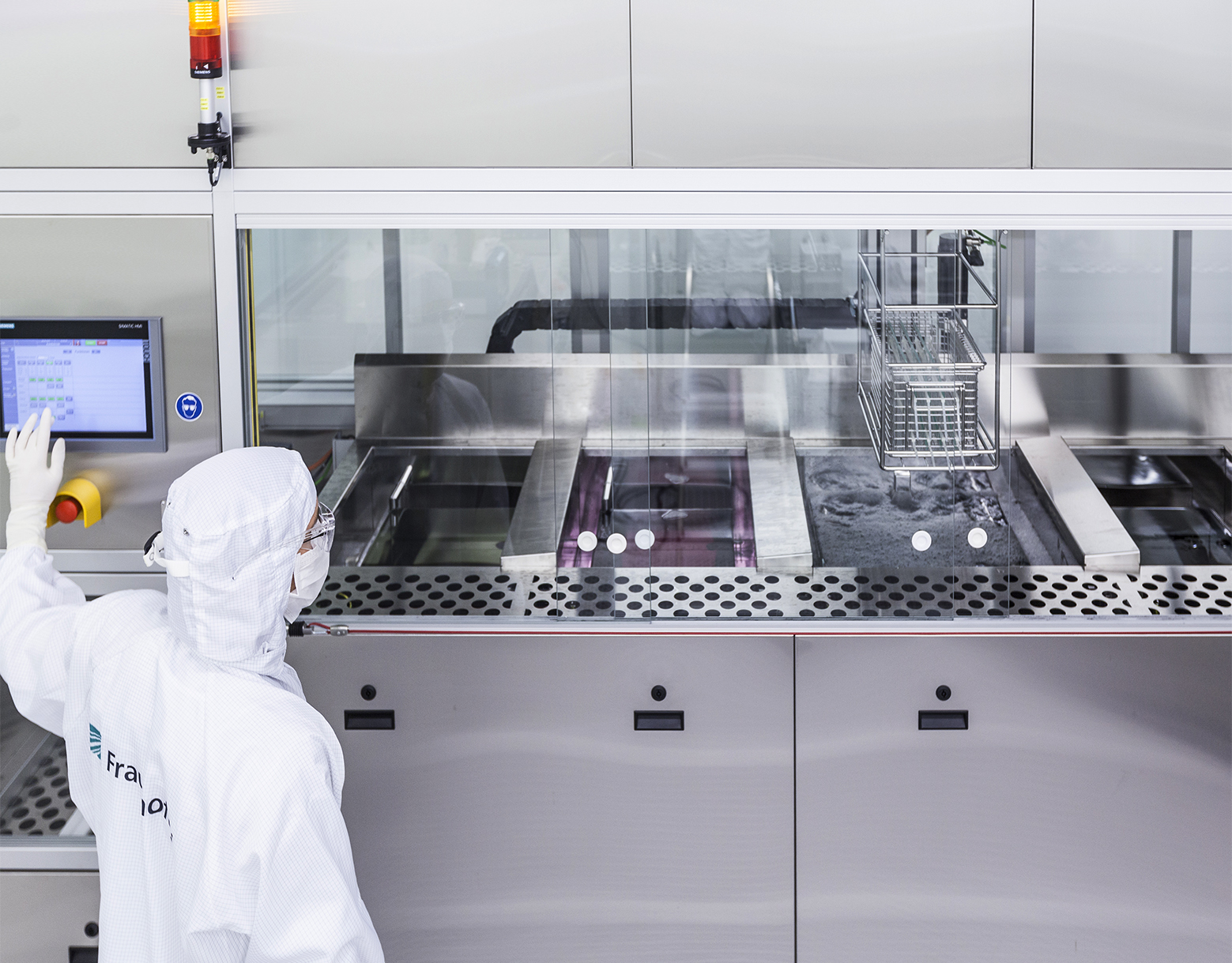
When component parts require cleaning, there is no uniform procedure to be followed. The most suitable cleaning process must be determined, which all depends on the material, industry and application at hand. For workshop components, it is often sufficient to remove organic residues such as fats and oils with a solvent. Aeronautic applications, in contrast, require extremely delicate cleaning procedures, for example with CO2 snow. Occasionally, a component has different, sometimes unknown materials or a complex geometrical design. This requires a combination a different procedures which must be conducted in a specific order.
Trial and error often helps
IPA scientist Max Metzmacher explains: “Here is where the majority of service providers fail, because they tend to either specialise in coarse cleaning or fine cleaning. However, Fraunhofer IPA possesses both the knowledge and the tools to also find a solution to this issue.” Some examples of these tools are an ISO category 1 cleanroom CO2 snow nozzle and highly efficient ultrasonic immersion bath with several compartments. A particular challenge is presented by cleaning prototypes or individual component parts. Here, the process is not integrated in manufacturing, as is the case for serial production. Threshold values and suitable processes must instead be ascertained first of all. Fraunhofer IPA is able to conduct complex tests and lab experiments as well as guaranteeing the required level of safety. “When the original idea doesn’t quite work, we simply try something new out”, Metzmacher explains.
Validating cleanliness
The actual cleaning is only part of the process. The level of cleanliness must also be verified and validated. In some industries standards have already been defined which stipulate specific test methods and threshold values. For example, VDA Volume 19.1 regulates the automotive industry whereas the ECSS (European Cooperation for Space Standardization) regulates the aerospace industry. Fraunhofer IPA has the instruments to conduct the analyses required here. Measurements using an electron microscope, gas chromatography or infrared spectroscopy are all possible, for example. If no regulatory framework has been established, the scientists support their partners in defining suitable standards. Furthermore, the scientists form committees in order to establish norms for various industries. These include the industry association “Cleanroom Suitable Consumables (CSC)” for consumable supplies in cleanrooms or Adhäsa, an association for adhesive cleanliness.
Clean packaging for clean transportation
Cleaned and validated components are not easily packed and dispatched in boxes. As Metzmacher explains, “The majority of components require a cleanroom in order to remain unsoiled. If they are taken outside of this environment and carried down the corridor, the threshold values will already have been exceeded.” Instead, the components must be wrapped in certified sheets and transported in a clean environment. In cases where the components are exceptionally large with complex geometrical designs, IPA scientists design suitable packaging to safeguard the clean status of the components.
Metzmacher summarizes things by concluding: “Our USP is that we are able to carry out the whole process chain, from cleaning through analytics all the way to packaging in ultra-clean environments.” It is because of this that the team has years of experience working for companies using components which are subject to the strictest cleanliness requirements. “Our customers include, for example, the aerospace company OHB Systems AG and the European Space Agency,«” the expert explains.