Smart solution for plastics processing
Condition and process monitoring implemented in temperature control systems
Temperature control systems play an important role in plastics processing. Products will only achieve the desired surface and properties if the temperature of the machining tools and the material is properly adjusted. With »Logotherm 4.0,« Fraunhofer IPA and Gesellschaft Wärme Kühltechnik (gwk) have together developed a solution that monitors the condition and process data of the temperature control system and sounds an alarm in the event of any anomalies. This decreases waste and increases process quality, while simultaneously optimizing maintenance.
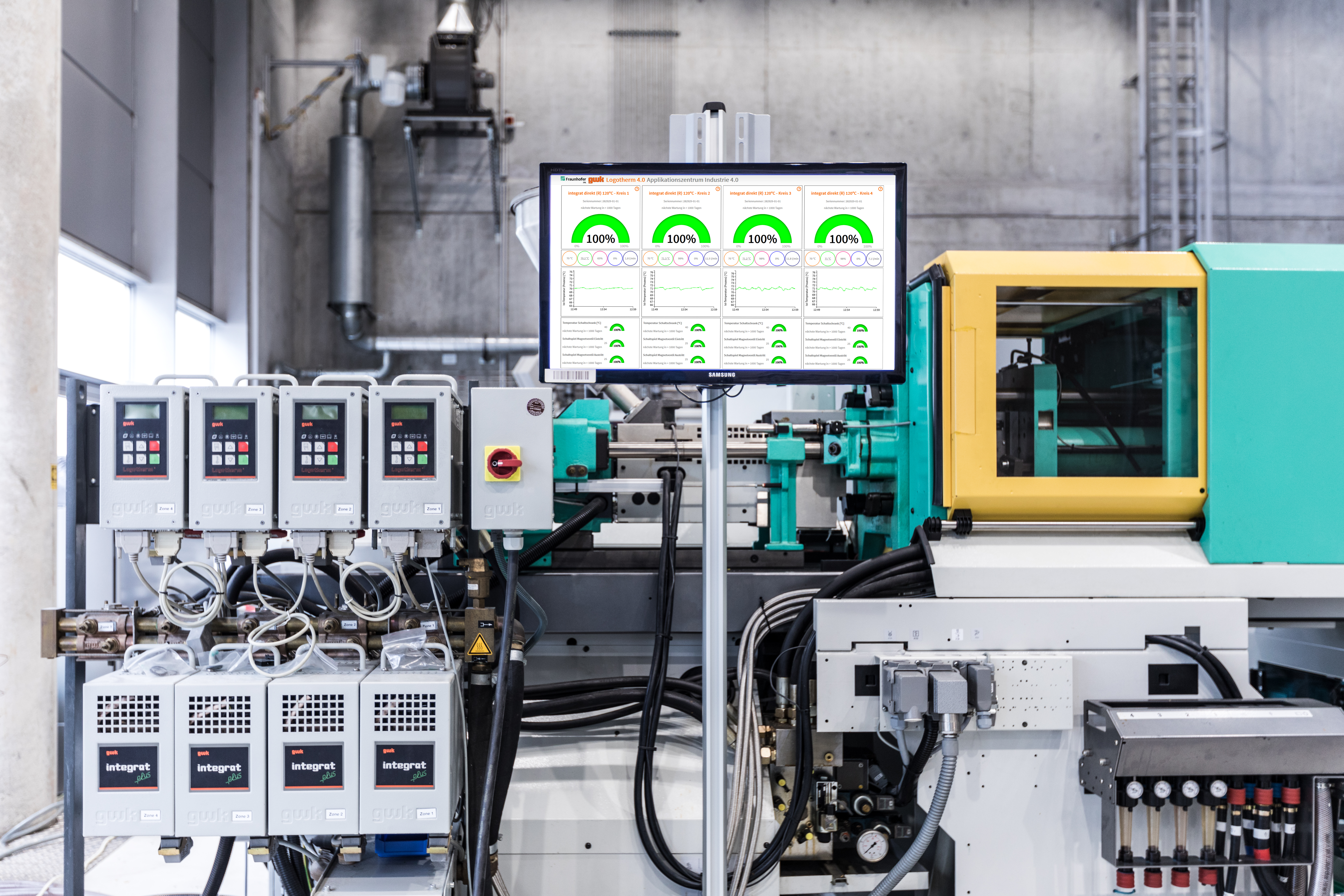
First, the researchers linked the gwk temperature control system to Virtual Fort Knox, a cloud platform developed by Fraunhofer IPA. With this link, Logotherm 4.0 collects the condition and process data from all machines within the plant. The information is displayed centrally via a dashboard in near-real time. IPA Project Leader Dennis Bauer explains: »This increases transparency in production. The person responsible can view the data from any machine live and doesn’t have to go over unnecessarily.
Proactively maintain equipment
The Industry 4.0 approach doesn’t just involve collecting data from production, it also means processing it in an intelligent way. With Logotherm 4.0, this happens via a Condition Monitoring Service that runs in the background. Dennis Bauer adds: »The application analyses data from the machine control. Errors and anomalies are shown on the dashboard.« The Fraunhofer IPA researchers have also integrated a notification service into it, which sends the responsible person a message automatically in the event of any problems. This means that defects can be identified and resolved more quickly.
The solution is also suitable for predictive maintenance. It can accurately determine the service life of the most important components such as pumps or vents using the condition data. This means that machines and equipment can be maintained proactively and downtime can be reduced. Logotherm 4.0 also improves the process quality. The responsible person can call up machine data for temperature, flow volume, pressure and performance. If any anomalies occur, the employee can readjust it quickly. Fraunhofer IPA researchers designed the dashboard in line with gwk’s specifications. Imminent issues are shown in yellow, while acute problems are red. The user interface applies the drill-down principle. Increasingly detailed information can be obtained by delving deeper into the three levels.
Solution opening up new business models
Logotherm 4.0 is suitable for all companies using temperature control systems for plastics processing. In principle, however, the condition and process monitoring could be applied in all industries. Dennis Bauer: »With this solution, companies can offer their customers a digital value-added service and restructure their business model.« For example, it would be possible to carry out maintenance remotely or supply replacement parts automatically. A demonstrator of Logotherm 4.0 has been set up at the Fraunhofer IPA Industry 4.0 application center.